As the world transitions towards cleaner and more sustainable energy solutions and the demand for renewable energy sources and electric vehicles continues to rise, the role of reliable and scalable battery plants becomes increasingly pivotal in powering the future. By 2050, more than 80 percent of new cars sold are expected to be battery-powered with the demand for lithium-ion batteries used in electric vehicles (EVs) projected to grow five-fold between 2021 and 2030.
China leads the way and accounted for approximately 70 percent of the global Li-ion battery capacity in 2023 and in Europe, Germany has overtaken Poland bolstered by Volkswagen’s battery cell gigafactory in Salzgitter built by Exyte.
The construction of a modern and cutting edge battery plant comes with its own unique challenges and considerations and in this article we will explore these essential factors from site selection and design right through to operational strategies and production.
When delivering a complex and challenging project build like a battery factory it is a good idea to start with the end in mind. It is generally accepted that the drier the clean room, the better the battery cell and the more constant the quality at the end. With that in mind, the clean room(s) become the core deliverable where everything is essentially built around them. It’s advisable to start with a dry-clean culture mindset from the very outset that will pay dividends as you begin to certify the production spaces and install equipment and will enable an ongoing operational culture for the facility.
It is vitally important that the humidity is kept at the lowest possible level, while high-level clean rooms are adequate for semiconductor manufacturing, they contain 30 times more humidity than the ultra-low relative humidity (RH) requirements for lithium-ion battery manufacturing. Uncontrolled humidity in battery plants will cause defects resulting in reduced product life, performance, overheating during charging, and potentially even cause fires.
One of the first steps for construction companies is to conduct a thorough site assessment. A long list of factors should be considered such as proximity to raw materials, topography, utility availability, electricity grid capacity, transportation access, local regulations, future labour force, environmental considerations, planning permission and community impact amongst others. Selecting the right site sets the foundation for a successful project and minimises risks associated with unforeseen challenges during construction and operation.
Collaboration and good decision making are vital in the design and construction phase and all stakeholders should have access to the right information at the right time. Often with these mega battery facility builds it is a joint venture between a carmaker and a supplier and the lines can get blurred between who’s in charge of what, who’s responsible for decisions, sign offs and different deliverables. That’s why it’s important to choose a construction management, turnover and commissioning software that all required stakeholders can access and will set the project off on the right path from the outset and for its lifespan. Confusion on this will cause schedule delays, rework and costs to spiral.
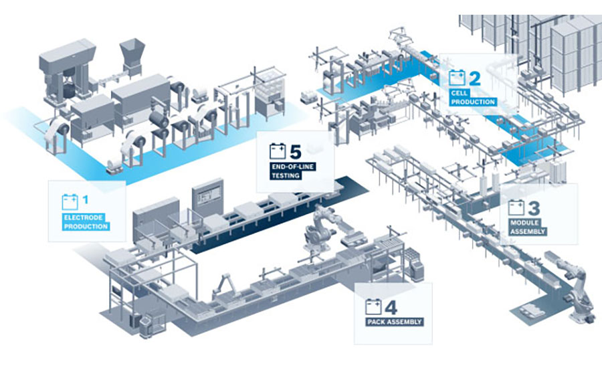
Illustration courtesy Bosch Rexroth Corp.
To enhance the material flow efficiency, boost productivity, and expedite time to market, it’s worth considering consolidating individual buildings into a unified, larger structure. This integration, while maintaining proper fire separation and life-safety measures, not only trims the site requirement area and minimises the need for conveyor systems but also lowers both construction and operational expenses.
Additionally, you should consider establishing a central “spine” within the plant. In the context of an electric vehicle battery manufacturing facility with separate cathode and anode lines, this separation naturally lends itself to incorporating a central spine. This not only serves as a pathway for people and equipment but also facilitates the distribution of utilities, reducing costs associated with feeding the manufacturing process.
Furthermore, constructing a battery plant requires specialised expertise in electrical and mechanical systems, as well as knowledge of the stringent safety and environmental regulations. Clients and construction partners/contractors should collaborate with engineering firms experienced in battery plant construction to not only ensure compliance with the industry standards but also help optimise the plant’s design for efficiency and scalability.
There needs to be an understanding of the nature of the chemicals and raw materials that are being processed to design the right kind of environment, and to determine the best building materials to contain them safely. Large scale gigafactories are a relatively new phenomenon to the construction industry, so experience and advice here is very valuable.
Speaking of safety, it is a top priority in any industrial facility, especially in a battery plant where hazardous materials and high-energy processes are involved. Implementing robust safety protocols, training programs, and emergency response plans is crucial to prevent accidents and protect the well-being of employees and the surrounding communities. With the right construction management software solution you can switch to digital and streamline everyday safety activities such as document management, permitting, risk assessments and method statement approval which is supported by powerful real-time reporting.
Efficient supply chain management is also essential to ensure a steady flow of raw materials and components necessary for battery production. Establishing strong relationships with suppliers, implementing inventory management systems, and diversifying sourcing options can mitigate supply chain risks and optimise your cost-effectiveness. Additionally, encouraging transparency and accountability throughout the supply chain is important to uphold your ethical standards and address potential social and environmental concerns associated with raw material extraction and transportation.
In conclusion, the construction of a gigafactory is a multifaceted endeavour that requires careful consideration of various factors, ranging from site selection and design to environmental impact mitigation and supplier collaboration. By addressing these considerations comprehensively and strategically, clients and contractors can enhance operational efficiency, sustainability, and long-term viability, contributing to the advancement of clean energy technologies and the transition towards a more sustainable future for all.
If you would like to hear more about how EIDA can help you with your next gigafactory build, speak to one of our expert senior consultants today.